Kjærrahvalen was designed by Trond Fredriksen and built in collaboration with the Kjærra Fossepark Foundation, the former Lardal municipality, and Høyskolen i Telemark – now USN – campus Notodden. The kiln stands as a monumental sculptural work with practical utility just a few meters from the Lågen river, in Kjærra Fossepark.
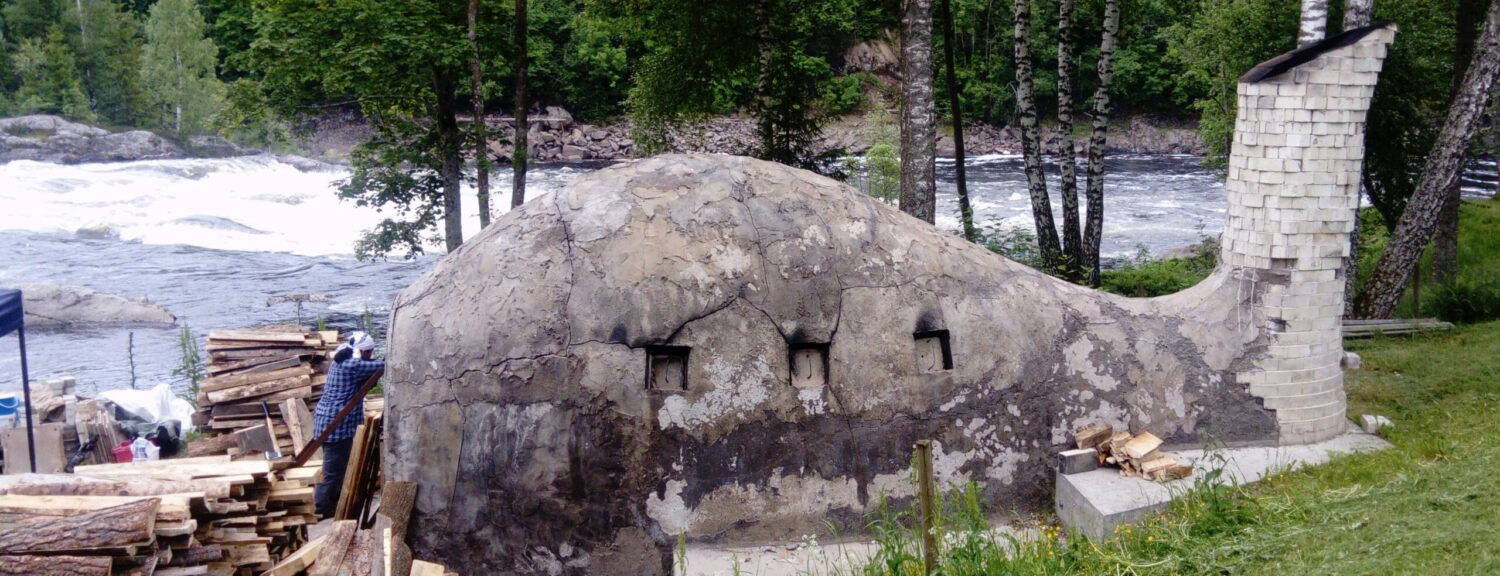
In 2015, the kiln was fired once to remove the internal wooden structure that supported the several thousand refractory bricks. In the autumn of 2016, Trond Fredriksen brought a group of students from Høyskolen i Telemark (now USN – campus Notodden).
The students spent about two weeks creating sculptural works and glazing the objects. The students also prepared for stacking (applying what we call stacking material – a material used to protect the base of the objects from sticking to the shelves). The objects were then placed in the damp kiln before it was lit. This group consisted of around 12 people.
The weeks we worked at Kjærra were damp and at times terribly cold, but nevertheless provided exciting experiences for the group. Not to mention that during the second night, 25 cm of wet snow fell! This was truly a baptism by fire, and those of us who participated are left with fantastic memories. Several of the original group have participated every year since 2016.
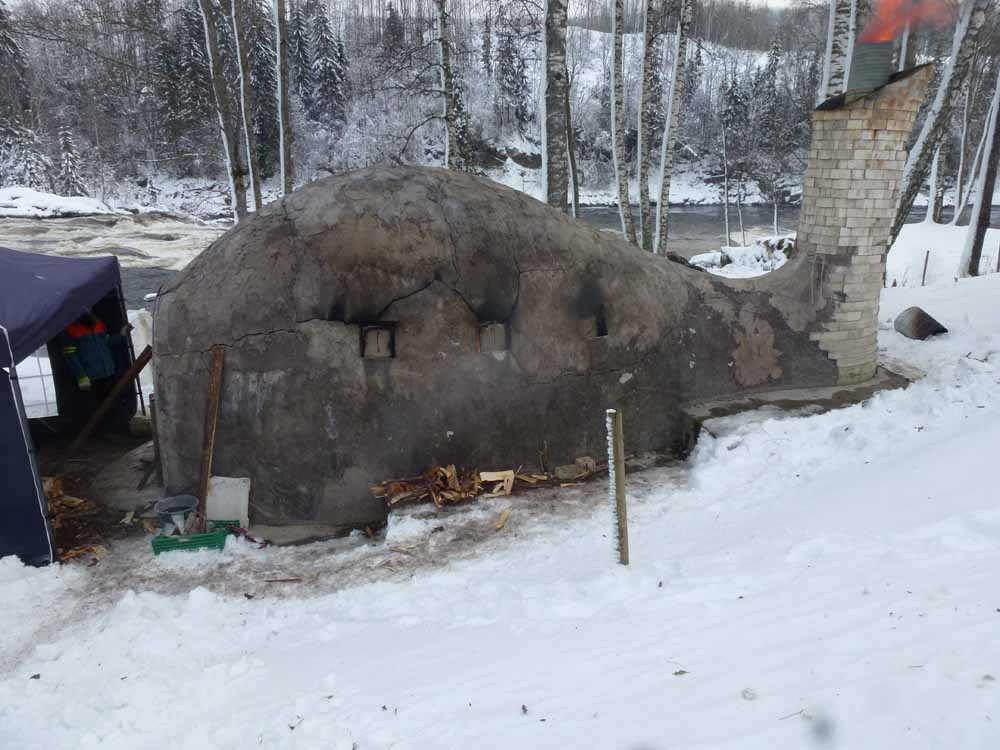
The kiln is Norway’s largest anagama kiln, the largest in Scandinavia, and the tallest in Northern Europe. The Kjærrahvalen Association organizes firing every summer from the end of June to the middle of July. It holds up to 21 cubic meters of ceramics! The highest point in the kiln can accommodate sculptures of more than 2.4 m. The internal width is also two meters or more.
Anagama can be translated to «cave kiln,» and is of an old traditional design. This type of kiln was developed in China and further spread to Korea and Japan. In our modern era, there are anagama kilns all over the world. In Norway, we have a few; the oldest was built in 1984 and is located in Ringebu. Kjærrahvalen is a publicly owned kiln and can be used by everyone. It is one of the few kilns accessible to the public.
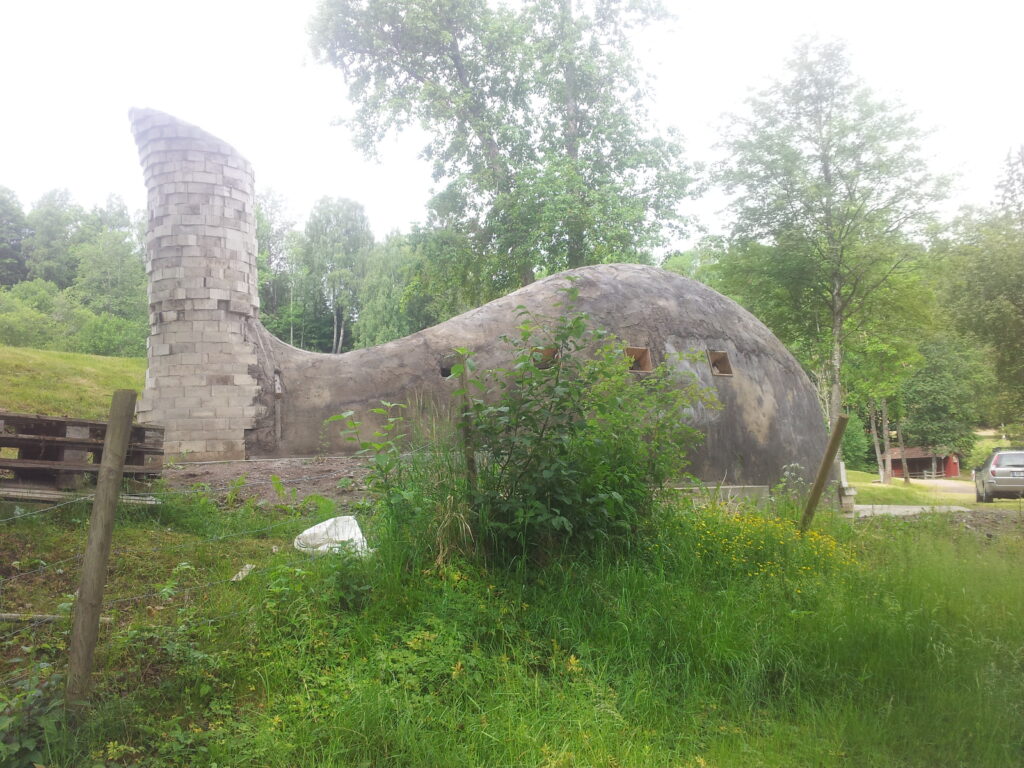
Wood-fired kilns give a distinctive effect on the surface of ceramics. Ash from the wood melts and creates a glaze on the ceramics. The flames are pushed between the objects and can create exciting color variations of yellow and orange. How the surface of the ceramic turns out depends on where it is placed in the kiln. Damage, marks, and color changes on the ceramics can tell where it was placed in the kiln, as well as which objects were standing nearby.
The kiln is filled with ceramics and fired for up to seven consecutive days. It uses between 30 and 40 cubic meters of wood for each firing. The wood we use is offcut wood that comes from local sawmills. In the months and weeks before firing, the wood is cut into lengths of up to 90 cm. All the wood thrown in from the sides at the end of the firing is split into thin pieces to release high heat. Large quantities of this wood are chopped with an axe in the weeks before, but also during the period we are firing the kiln.
During each firing project, we work to raise the temperatures to between 1250 and 1300°C. When the firing is complete, the kiln is completely sealed with pyro-thermal insulating fiber so that the temperature drops slowly. Well-insulated, it stands to cool for about a week before we open it.
It is difficult to predict the results in the kiln before we open it. Many factors influence how the result will be. Therefore, this type of ceramic firing is very exciting for ceramicists!
The heat from the flames evaporates the water in the ceramics, and chemically bound water is pushed out at around 600°C. At about 1000°C, the quartz in the body is converted to glass, while the ash from the wood adheres to the surface of the ceramics. At about 1200°C, parts of the ash will begin to melt. The quartz in the ceramic reacts chemically with the ash and forms a glaze, and substances in the ash contribute to different textures and colors. Which color appears depends on the temperature, the type of wood we are firing, the type of clay and its content, as well as which other glazes and clays are nearby. Traditionally, we have certain glazes that are made for wood firing. Among the Japanese glaze types are Shino glazes (meaning «snow on the peaks» in Japanese), Tenmoku glaze, and Celadon glaze. They give white, brown, dark, blue, green, yellow, orange, brown, turquoise colors. Cobalt glazes give intense blue colors. In such kilns, it is common to use stoneware clay and porcelain clay as they withstand the high temperatures.
When the kiln is opened the first weekend in July, all objects are systematically taken out of the kiln. Each shelf and each rack is marked and documented with pictures and video. All stacking material is cleaned of glaze residues and ash, stacking material, and other things that have stuck during the firing. We notice that it is the work and activity around the firing that generates the most enthusiasts, and many get «hooked» every year. The ceramics can be purchased directly from the kiln. When it is opened, the Kjærrahvalen Association usually holds a market and exhibition of the ceramics. Throughout the entire process, you can get close and experience the inferno in Kjærrahvalen.